Overview:
Occupying an entire city block in the bustling Midtown Atlanta, the 1105 West Peachtree development is a 1.75 million square foot mixed-use project featuring three high-rise towers interconnected with a parking, retail, and amenity podium deck. The development features a 410-foot-tall, 31-story office tower, a 16-story, 178-key culinary themed boutique hotel, and a 20-story condominium tower offering 63 luxury units. The three towers are interconnected through an eight-level parking podium topped with a landscaped amenity deck with indoor and outdoor swimming pools. The podium structure also includes 20,000 square feet of retail spaces across the lower levels. The development is constructed to bridge over an existing underground subway tunnel used by MARTA which runs through the project’s site beneath the podium and condominium and hotel towers.
The Office Tower:
Anchoring the development is the 31-story office tower, Atlanta home for Google LLCI, constructed of cast-in-place concrete framing and featuring a dramatic architectural steel exoskeleton. Totaling 675,000 square feet of class A+ office space, the tower offers 27,000 square foot efficient, column-free floor plates and provides panoramic views of the Atlanta cityscape.
The typical office floor construction consists of conventionally reinforced concrete slabs with junior beams spaced at more than 15’-0” on center and supported on post-tensioned concrete girders at approximately 30’-0” on center. The use of post-tensioning reinforcement enabled offering an efficient, column-free space spanning 46’-0” between the floor central core and the perimeter columns while limiting the overall structural depth to 21”. Also, this floor framing system provides flexibility for future tenant improvements.
The parking areas below the office tower utilized a different framing system consisting of 7” thick one-way post-tensioned slabs spanning up to 32’-0” between 30” deep post-tensioned beams with up to 65’-0” spans between columns. Thicker slabs are used at parking floors receiving waterproofing protected with a concrete topping slab. At the top of the parking podium, the landscaped amenity level framing system consists of 9” one-way post-tensioned concrete slabs supported on post-tensioned concrete beams with depths of up to 48”.
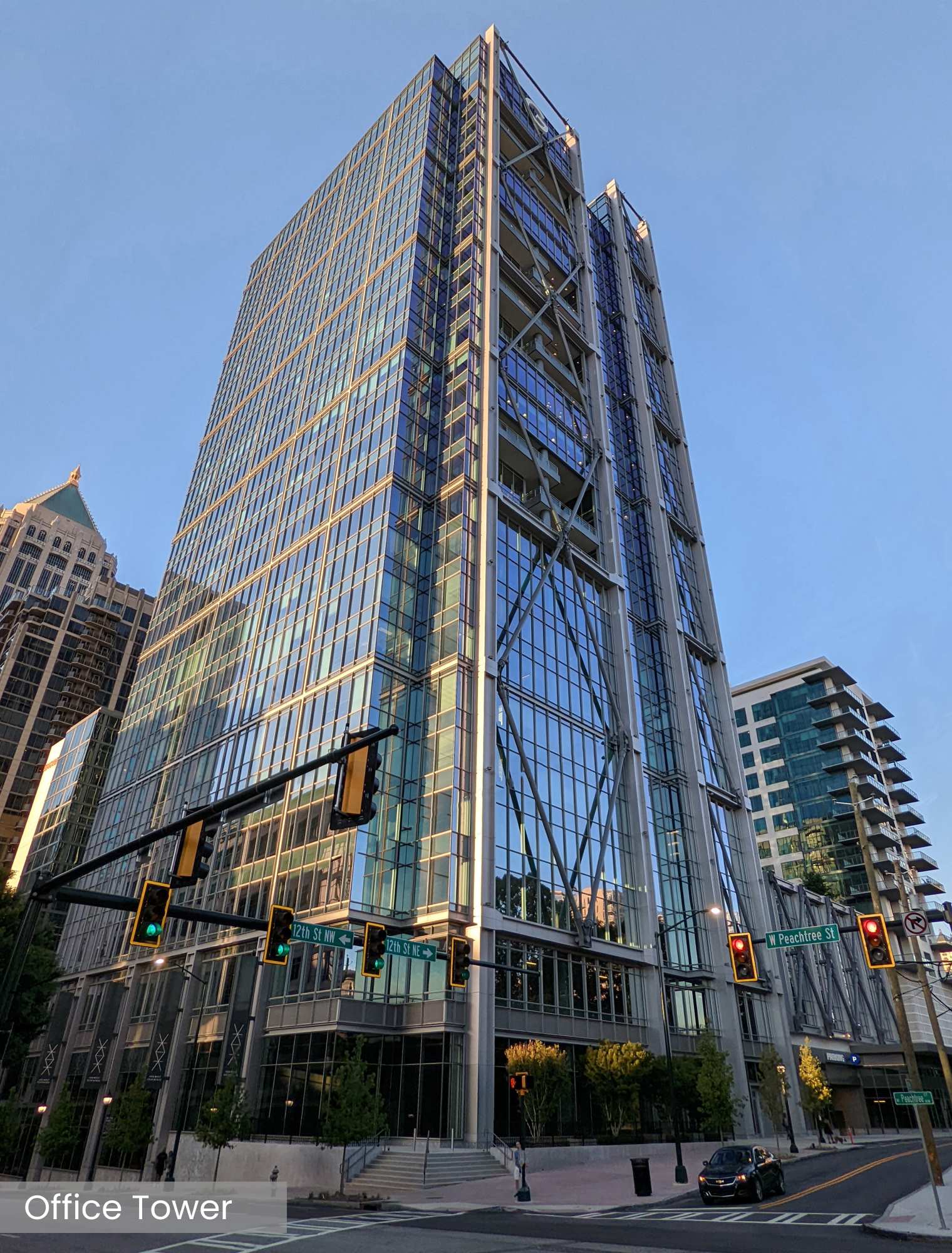
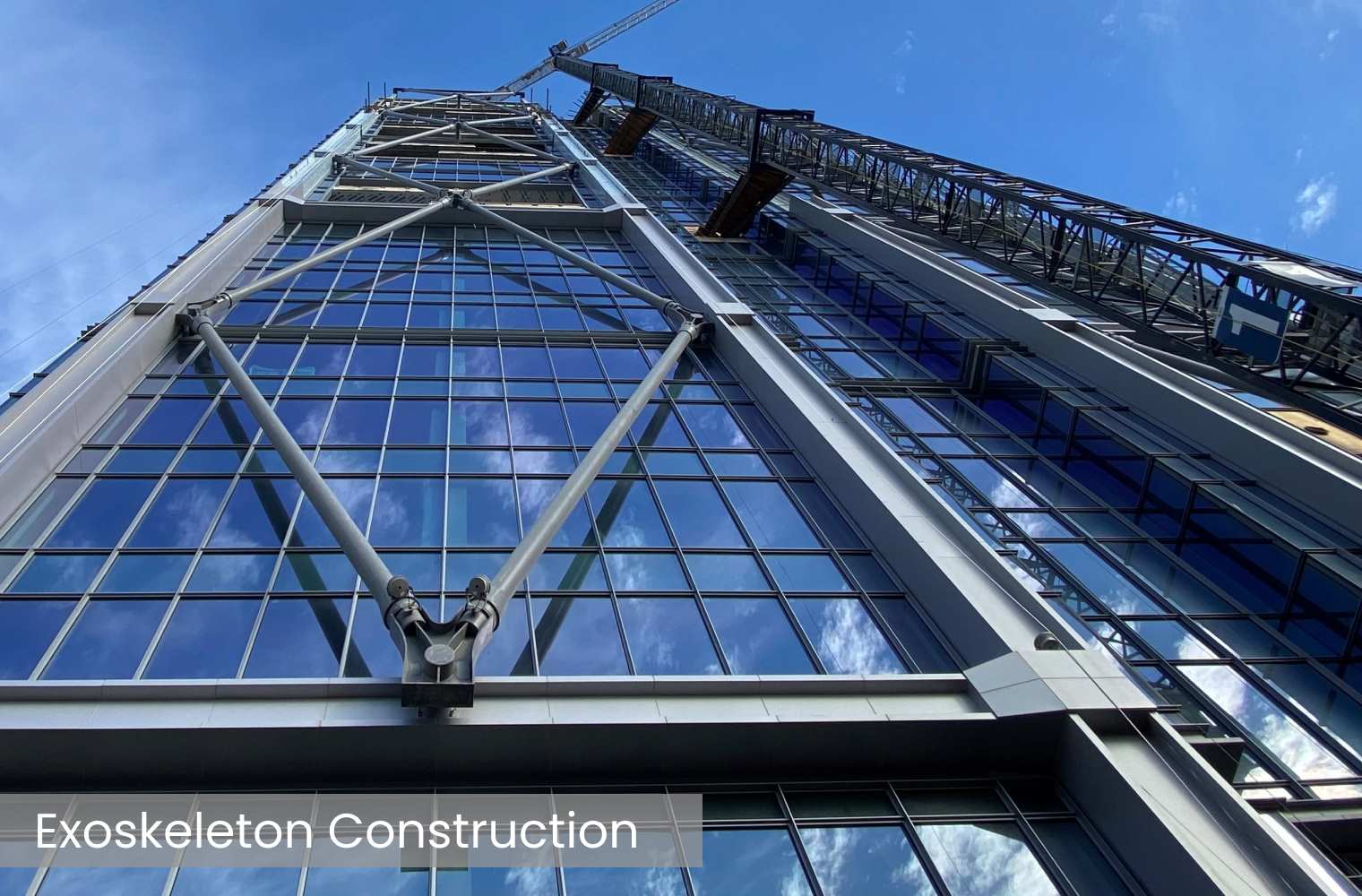
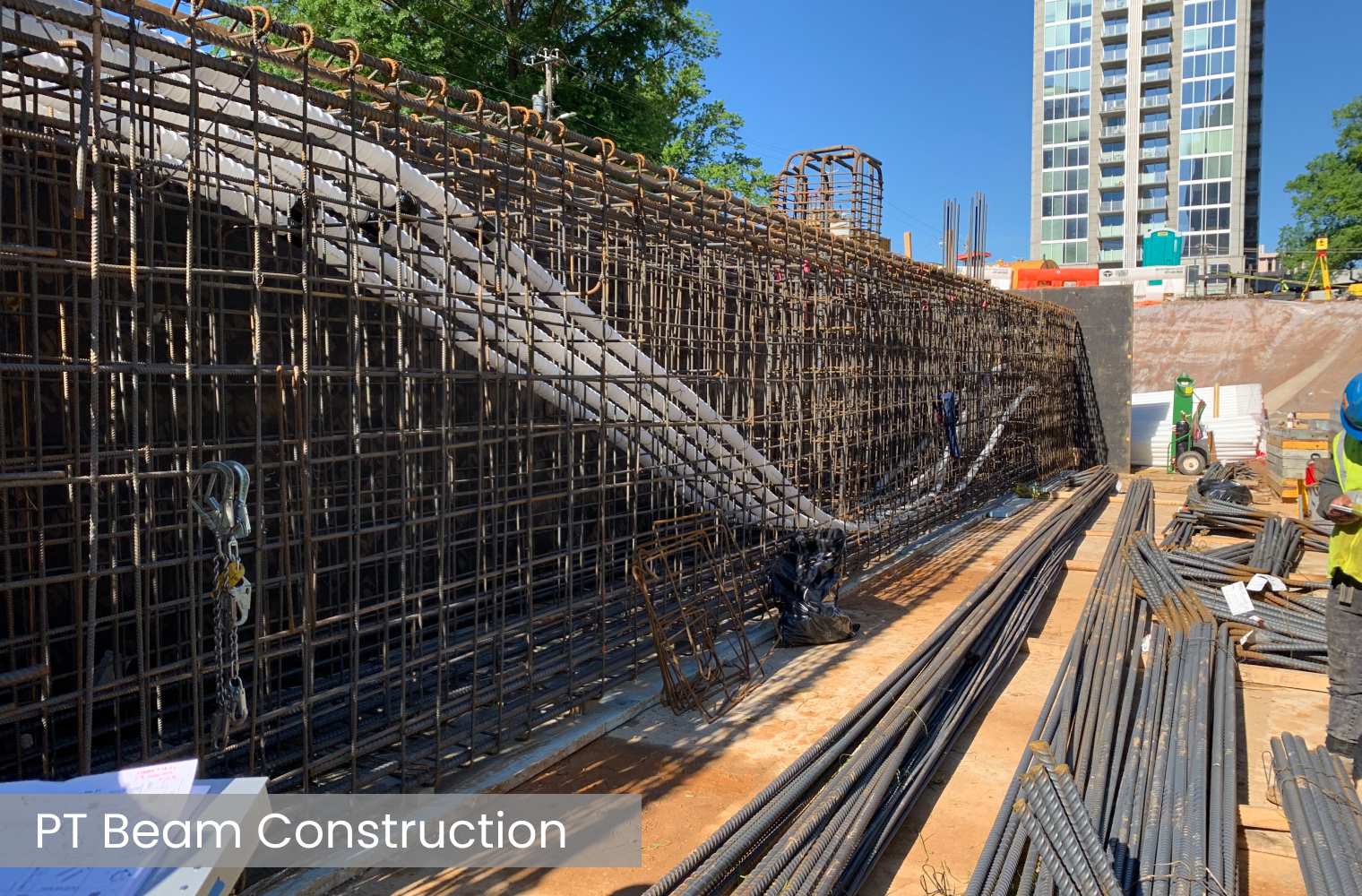
Reinforced concrete shear walls at the central core constitute the major portion of the building’s lateral force resisting system and are supported on a six-foot-thick concrete mat foundation on drilled piers ranging from 78” to 96” in diameter. Much of the building’s lowest basement level is surrounded by concrete retaining walls including an underground tunnel connecting the basement level to the adjacent hotel back-of-house space.
The office tower features a distinctive 420-foot-tall, geometric steel exoskeleton at the exterior of the glass façade on the south elevation in addition to secondary exoskeletons on the office north elevation and podium exterior. The diagonal members of the exoskeleton are supported on steel outriggers welded to steel plates embedded within the main concrete frame. The end connections of the diagonal members to the gusset plates were carefully designed to accommodate different building movements. The office tower facade exoskeleton extends 39’-0” above the roof and continues along the roof to create a building crown that includes a 25’-0” tall, glazed screen wall. The roof concrete framing was efficiently designed to support this free-standing crown and screen wall system. At night, the exoskeleton is illuminated by multicolor LED lights, adding to its overall uniqueness.
The Hotel and Condominium Towers:
The typical framing system for the condominium and hotel tower floors utilized a two-way post-tensioned flat plate system. The condominium tower slabs are 8” thick spanning up to 31’-6” between columns while the hotel slabs are 7.5” thick spanning up to 27’-0” between columns. The use of the post-tensioning flat plate system provided a consistent, architecturally unfinished soffit at these floors, reduced the structural depth, and offered efficient floor construction. The parts of the parking podium beneath the condominium and hotel towers also utilized a two-way post-tensioned flat slab framing system. The hotel tower also included several column-transfer post-tensioned girders to satisfy the architectural space planning requirements.
Design Challenge – Protecting Existing MARTA Subway Lines:
The most challenging aspect of the design was that the project site is located directly over the red and gold lines of the Metro Atlanta Rapid Transit Authority (MARTA) underground rail tunnels. Much of the condominium tower footprint and parts of the hotel tower and parking podium are located above these two MARTA tunnels. As a result, 13 major post-tensioned transfer grade beams supported on drilled pier foundations were designed to transfer 33 building columns and 3 shear walls above the subway boxes to drilled piers outside of the subway tunnels’ non-encroachment zone.
The transfer grade beams have spans between 56’-0” and 63’-4” and vary in depth between 84” and 120” and in width between 66” and 96”. The beam dimensions were controlled by the uneven finished ground floor and grade elevations and the limited headroom above the variable elevation, non-encroachment zone of the subway tunnels. While unbonded post-tensioning reinforcement was used elsewhere on the project in general, a bonded post-tensioning system was used for these transfer grade beams for added durability. The use of post-tensioning for these transfer beams provided an economical design that satisfied the dimensional constraints.
The majority of these large dimension transfer beams were poured during the spring and summer months between May and August. As such, a mass concrete thermal control plan was prepared and coordinated with the construction team. When cement and water are mixed, their chemical reaction generates heat. Larger volumes of concrete, such as the deep transfer girders, can generate enough heat to exceed strict thermal limits and can lead to concrete cracking. To meet the strict thermal requirements through placement and curing, liquid nitrogen was used to cool the concrete temperatures during these warmer months. Without the liquid nitrogen usage, the maximum internal temperatures would have likely exceeded allowable values.
Conclusion:
1105 West Peachtree is an impressive prime city-block development that displays widespread use of efficient concrete construction and dramatic exposed structural steel. The structural design contributed heavily to the overall success of the project, including economics, efficiency, durability, and aesthetics. Efficient design allows each tower to offer luxury amenities, convenience, and panoramic views to their tenants and guests making them welcome features of the Midtown Atlanta skyline.